Match Center Romania is at the forefront of a burgeoning industry following the recent legalization and proliferation of sports betting in many places. As one of the hubs for this activity, there has been much discussion around how this development might affect society. Sports betting undoubtedly provides entertainment value and …
Category: Uncategorized
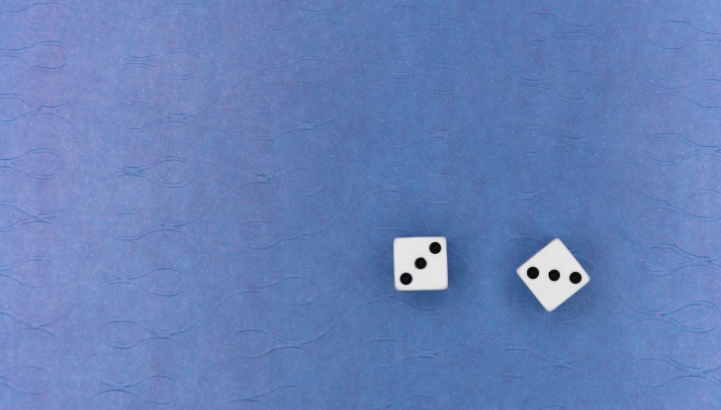
What is a Betting Syndicate?
Betting syndicates, also known as betting groups or betting pools, have gained significant prominence in the realm of sports betting. These organised collectives bring together individuals who pool their resources, knowledge, and expertise to analyse betting markets, identify value opportunities, and place wagers as a unified entity. By combining their …
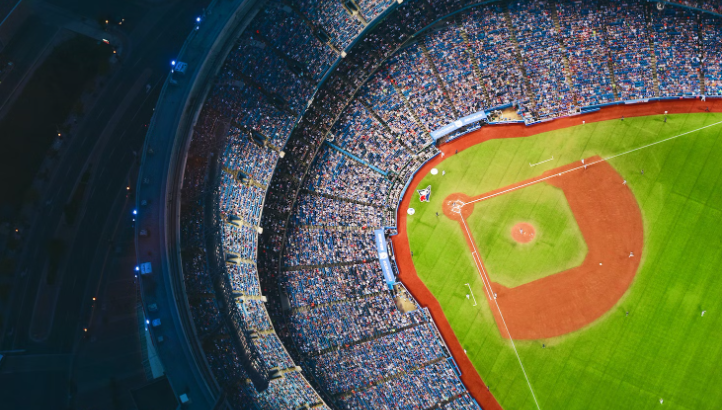
Why Do We Need Sports Museums and Hall of Fames
The preservation of sporting heritage is a vital aspect of cultural conservation. Sports museums and halls of fame play a crucial role in this endeavor. This article will explore the significance of these institutions, their impact on society, and the ways they contribute to the understanding and appreciation of sports …
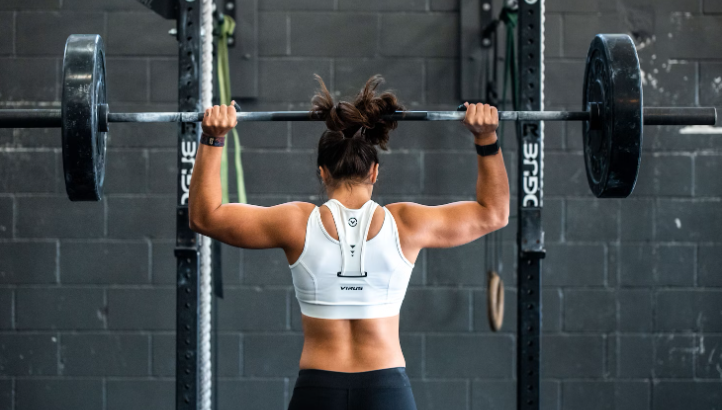
How Sports Can Drive Social Change and Community Development
Sports have long been a source of entertainment and competition around the world. However, sports can also be an effective tool for enacting social change and strengthening communities when utilized properly. This article explores the many ways that sports can drive positive impacts beyond mere entertainment value.
Promoting Health and
…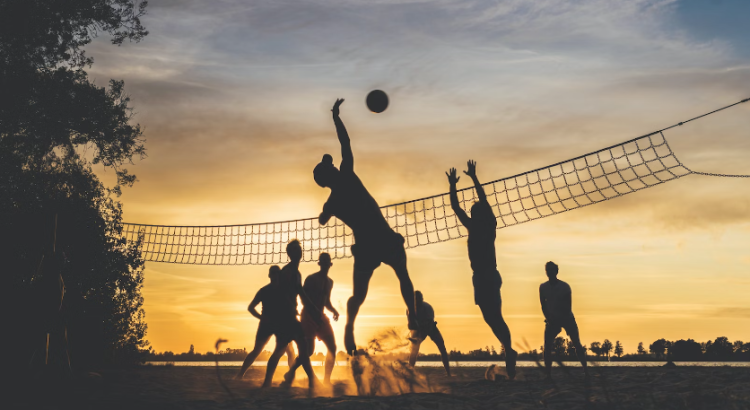
Technology’s Role in Evolving Athletic Performance
The world of sports has undergone a significant transformation with the advent of technology. From training methods to equipment design, technology has played a pivotal role in enhancing athletic performance. This article will explore the evolution of sports technology, its impact on various aspects of sports, and how it continues …
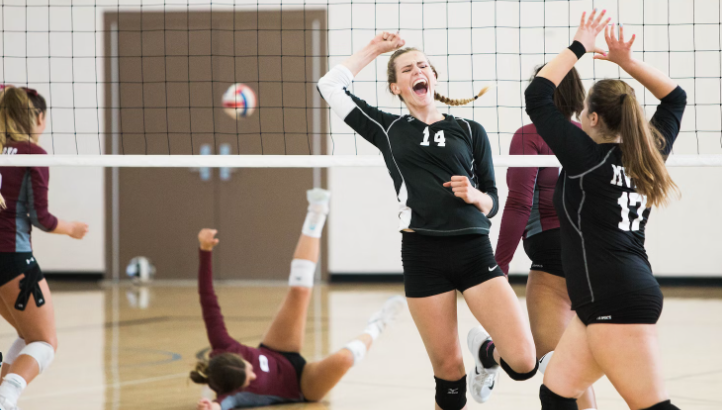
The Game Changers: Athletes and Their Societal Impact
Sports have long been an integral part of societies around the world. Beyond entertainment value, sports and athletes have had a profound influence on culture, politics, and social progress. This article examines the wide-ranging impact top athletes have on society and uncovers the unique power they hold as role models …